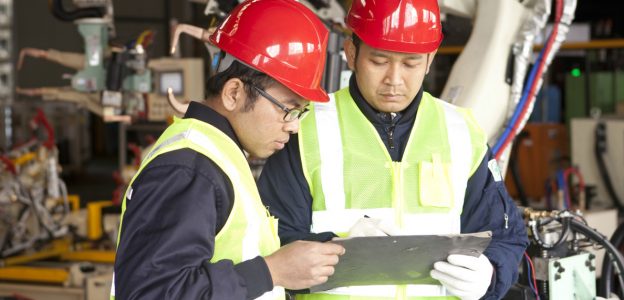
03 Jun Be Smart: Safe Restart
Re-starting Chemical Production Facilities Post COVID-19 Restrictions
As a result of the COVID-19 pandemic, many chemical production facilities around he world have been shut down for extended periods, experienced limited production capabilities, or law staffing conditions.
As companies begin reopening, it is critical that facility operators conduct pre-startup safety reviews, and take into account the unique circumstances at many sites due to this pandemic. In the chemical industry, including maintenance, inspection, retrofit, upgrading and others.
It is uncommon for an entire plant to be shut down, and even more uncommon for a plant to be shut down for weeks, potentially without staff onsite conducting preventive maintenance and inspections.
It is important to remember that a significant number, likely the majority of chemical incidents occur during startup. Process safety incidents are 5 times more likely yo occur during startup as compared to normal operations.
Prior to restarting any process, consider conducting a pre-startup safety review, to reassess hazards that may exist due to changes that may have occurred during the shutdown period.
A pre-startup safety review can help companies evaluate any additional impacts due to complications associated with complete shutdown that might impact startup procedures of any or all processes. For instance, auxiliary systems, normally not concurrently in shutdown may only come online for a short time prior to individual processes being restarted.
Some examples of impacts to auxiliary and production processes that might need to be considered include:
- Outstanding preventative maintenance due
- Outstanding inspections due
- Issues with lubrication systems
- Loose fittings, and equipment that may have become purged or de-inventoried
- Corrosion
- Compressed air systems, especially moisture accumulation
- Utility reliance (electricity, water, steam)
- Safety system functionality (including fire protection systems)
- Gas-detection functionality
- By-passed or disabled alarms and notifications
- Instrumentation stuck open/closed due to non-use
Exercise caution when performing startup operations, consider conducting assessments to determine when equipment is ready for operation, and give priority to restarting those operations with life safety functions, such as fire protection devices. Safe restart procedures will vary by company, and often involve great detail, but some general elements a company might include within its safe restart approach are outlined in the four steps below.